A new generation of 3D printer heaters, spiral heaters, is expected to be used more and more in 3D printing in the coming years as they offer better control and consistency. Let’s see why spiral heaters are meant to be the next big thing by going over the history of hotends and heating cartridges.
A bit of history
3D printer hotend has come a long way. Starting with the first design from Adrian Bowyer, then to the very famous J-Head, things have changed and improved over each new generation.
NiChrome wire
If you check back in 2007, the Darwin 3D print was one of the first. Created by Adrian Bowyer, it uses the “Thermoplast Extruder”, one of the first, most effective, and simplest hotend.
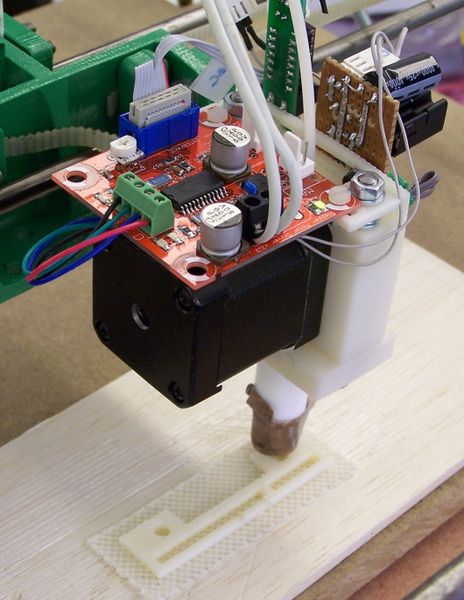
By looking at the heater section, you’ll realize that this hotend uses a NiChrome wire. It’s a resistive wire very commonly used in heating elements. It’s a very efficient and reliable solution, as the purpose of Nichrome is to heat, and its maximum operating temperature is way beyond what we use in 3D printing.

If you look closely, you can see yellow fibreglass insulation on the heating wire. Other hotends with similar designs used bare Nichrome wire. Extra care was needed as shorts with the wire could make the hotend not usable. More insulating and planning was required with bare wire.
The High Temperature Resistor
The J-Head has been one of the most popular hotend. It’s well designed, easy to use, and performs incredibly well. It’s one of the first hotend to use PEEK as its main material. The machining complexity and number of components were kept at a minimum. The model you might have seen is the J-Head Mark V-B, with brass heater block and grooved PEEK body.

This design uses a Riedon resistor. The specs are 5.6 Ω, with a maximum dissipation of 5 W. The maximum rated temperature is 250 °C, which is good for printing most polymers. The maximum temperature right might not be well adapted for our application, however, as the data sheet suggest lowering the power to 0% at this temperature:
The big improvement of using a high temperature resistor is that you could assemble it in a few minutes, and change it in about the same amount of time if it fails. Kapton tape was most often used to hold the resistor in place, which made it simple for anybody to use.
The Heater Cartridge
Around 2012, we started seeing more and more heater cartridges in 3D printers. For example, the delta 3D printer BerryBot3D included them with their hotend.
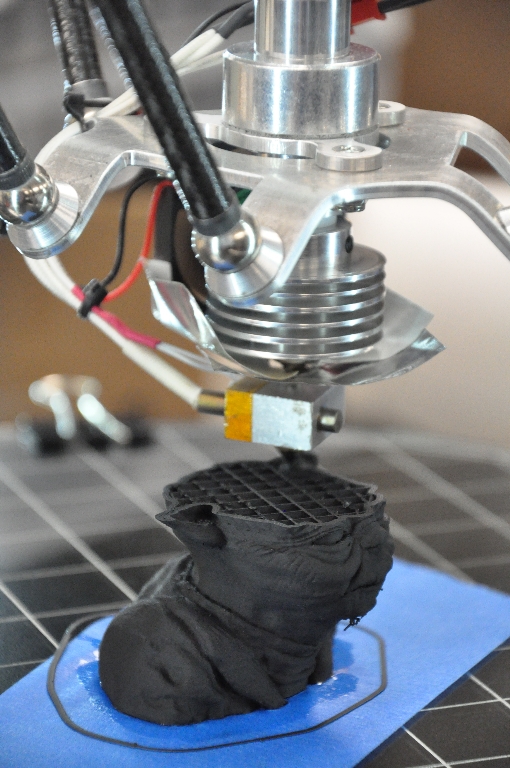
These cartridges were well adapted for the situation. The inside contains a heating wire, insulating ceramic, and the housing is in steel. It’s a self-contained heater available is roughly the same format as the heating resistor. People started swapping their J-Head resistor with this heater cartridge.
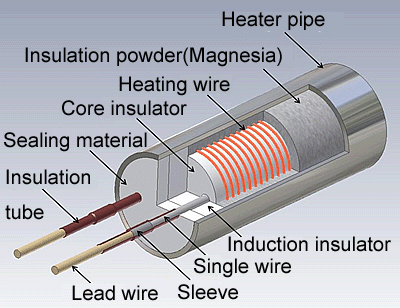
The need for improvement
All the previous had their strengths and weaknesses. But each of them was an improvement over the previous solution.
- NiChrome wire
- 👍 Designed for heating
- 👍 Powerful
- 👍 Cost effective
- 👎 Complicated to install
- 👎 Required putty
- 👎 Risk of shorts
- Resistor
- 👍 Simple to install
- 👍 Cost effective
- 👎 Limited in power
- 👎 Limited in durability
- Heater cartridges
- 👍 Simple to install
- 👍 Powerful
- 👎 Costly
Manufacturing challenge
The simplicity offered by the resistor and the heater cartridge led to the heater block. The heater block is a thermally conductive piece made from aluminum, copper, brass or steel designed to transfer the heat from the heater cartridge to the nozzle, to the polymer.
We’ve seen quite a lot of different designs over the years, with the heater in either a parallel direction or perpendicular. Same for the holding methods: Slot, threads for set screw, press-fit, etc.
As you can guess, these constraints can make a simple part more and more complicated. The costs will be directly proportional to this level of complexity.
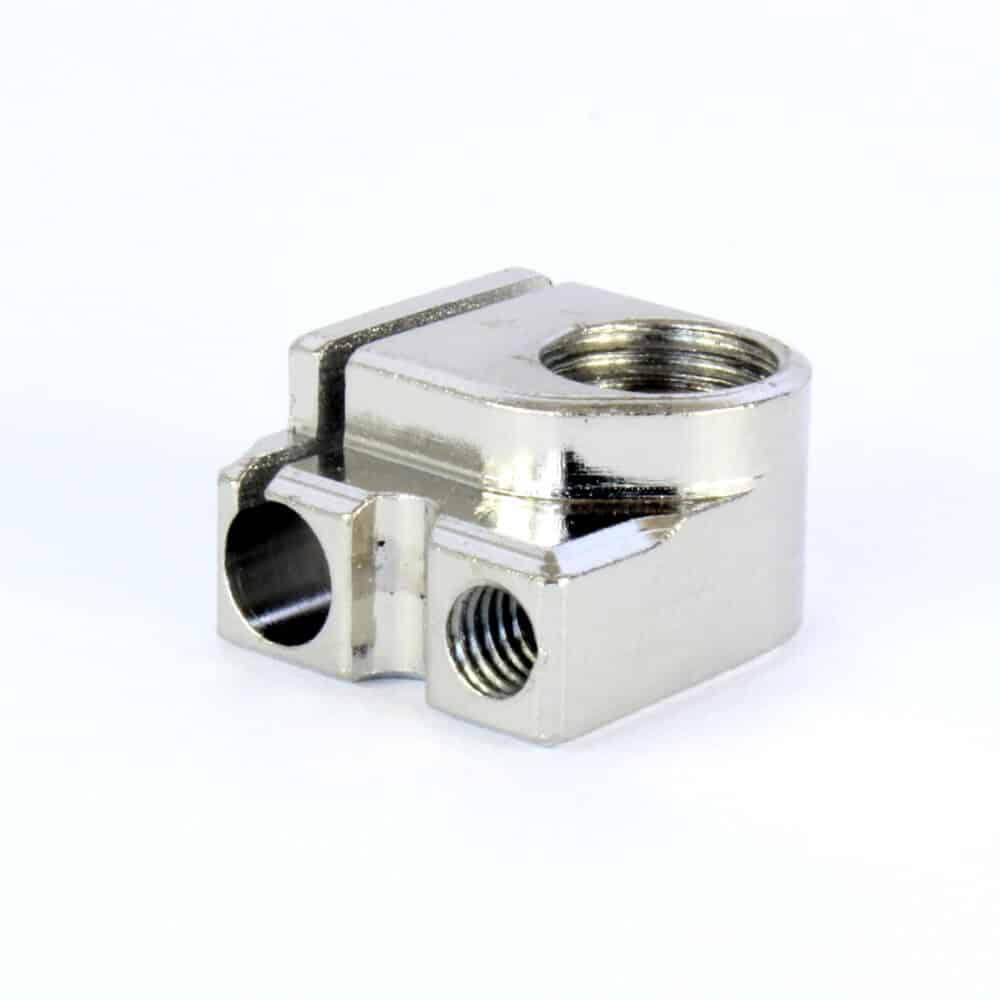
Temperature uniformity
Another weakness is the temperature uniformity. By considering the entering material as a cold material absorbing heat from the center, having a heater on the side only is suboptimal. The further you’ll get away from the heater, the colder it will be. Consider a quick analysis with the following parameters:
- input polymer (PET) at 35 °C at 5 mm3/s
- 20W heater
- 5 mm/s wind in one direction (like if the head was printing slowly)
Adjusting the temperature graph from 245 °C to 255 °C, you can see how the top region, the right section away from the heater, and the nozzle are much colder than the heater.
The new solution
Temperature uniformity is critical for printing accurately. Printing too hot, the polymer will degrade, printing too cold, the filament might be very hard to extrude. Having a 10 °C gradient over a small 15 mm melted length can be problematic. This temperature gap will increase a lot more over high temperature polymers such as PEI and PEEK.
Cylindrical Melting Zone
Since the development of our new high flow extruder (Typhoon) and our pellet extruder (Pulsar), we decided to shift our new design toward a more logical melting zone shape. Since the polymer follows a round hole, why not make the heated block a heated cylinder? By using this design, the heat travels naturally toward the center, when the filament absorbs it. The distance between the heater and the polymer is always the same, ensuring maximum uniformity across the melting length.
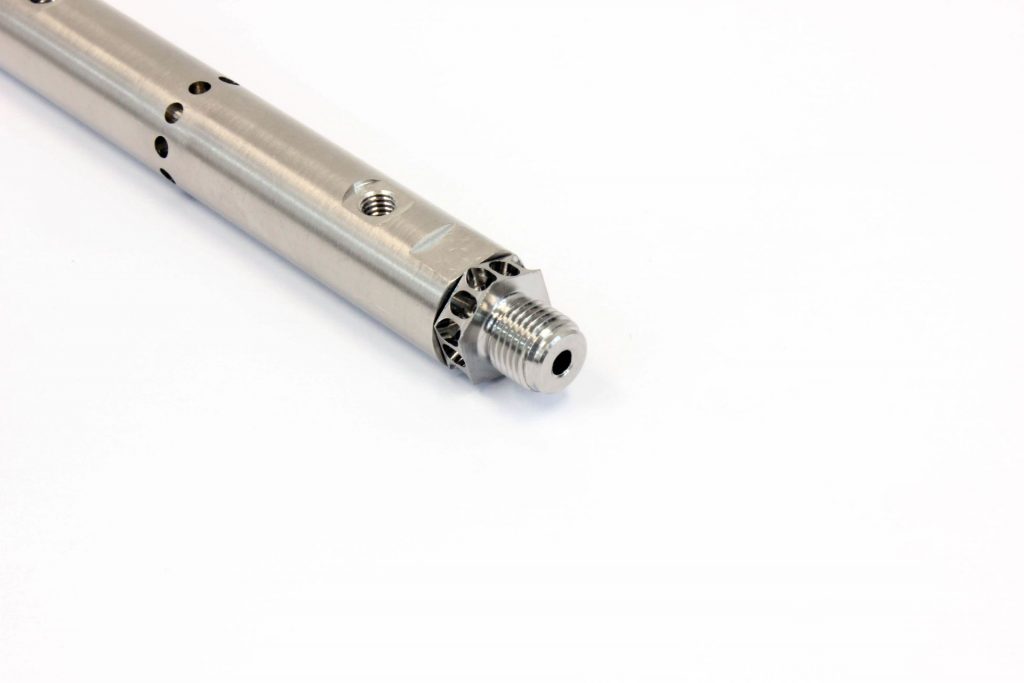
Spiral heater
The cylindrical melting zone also requires a new type of heater. Luckily for us, there are plenty of options for high temperature tube heating.
We ended up choosing the spiral heater type. It’s simple to customize, which allows us to choose the optimal shape and form factor for our application. By choosing the right number of turns, spacing, and power density, we managed to optimize the heater to get an even heating region through our long melting zones.
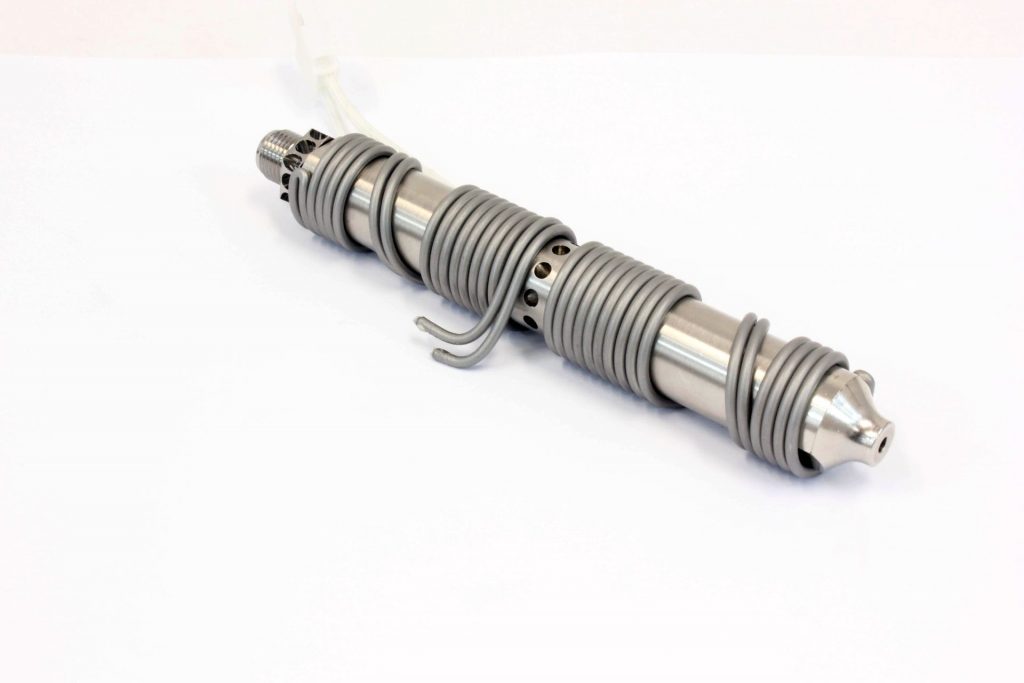
Multiple heaters
The extra long melting zone required for high flow has some new challenges. As you’ve seen previously, the 10 °C delta on a 15 mm length can quickly get worse over more than 100 mm. The picture below shows a single heater acting on the body when extruding 200 mm3 of PET per hour. The temperature difference is critical, ranging from 150 °C to 250 °C.
After running optimizations, you can keep the temperature with a much narrower temperature gap, perfect for printing consistently.
In summary
We’ve seen how 3D printers have evolved over the years, from the NiChrome wire in putty to the heater cartridge. The big temperature difference through the heater blocks showed a clear need for improvement. This is where the cylindrical heaters and spiral heater come: better temperature uniformity, better power distribution, simplified machining.
12 Comments
So the hotend is too long for most home printers, and likely too expensive.
Yes, exactly. The Typhoon is designed for high volume extrusion. It won’t fit on a small printer.
Same goes for the spools, at 1 kg / hours, you’ll need something bigger than 1 kg spool! Definitely not for home printers.
This is great, keep up the great research you guys!
Thanks! Hope you liked!
The spiral heater design is a cut & paste from Osco Inc., a company making injection molding components. These heaters are great, and a personal favorite for miniature heating element design (the osco nozzles really look well made and well designed, but I bought these as surplus so can’t comment on function, I used them in other projects). https://oscosystems.com/product/se-84/
My comment is this: thank you for getting around to doing what in my opinion was the necessary next step. To the DIY community: these spiral heaters aka nozzle heaters aka miniature heating elements and many other convoluted jargon bendings on ebay are difficult to find as they seem to resist intuitive naming, but once you get one, they are extremely versatile, bendable (within reason), and a wire brush dremmel attachment makes them as pretty as bismuth crystals.
It made my day to see these beauties make a debut on 3D printers!
You are right, the spiral heaters are indeed used in molding components. The name I see the most often is “Hot Runner Heater”. Most of them are quite big however, by standard. They need to be customized for our smaller application.
Thanks for your support!
You should use heater bands with three or 4 heating zones and set point controllers for each zone I have run over 50 large to small manufacturing extruders from blown film’s to filaments with over 20 years in and experiences from design to r and d and silo to skid productions in fda iso environments
From operator to project manager maintenance manager csr and so on..
My experiences maybe of interest and I could use help on the modelling side
I know all the high temp materials today
Let me know if your interested in learning more
Kevin
Thanks for your comment, Kevin.
Indeed, the band heater are an interesting solution. While most of them are good up to 400°C, it was getting costlier to get the few ones that resist 500°C.
Also, with our small tube size, most manufacturers were unable to match our requirements.
Finally, making using coil heaters allowed us to control heat density, something much harder to do with band heaters.
Hot-End manufacturers now reinvent the wheel 🙂
That’s sadly far too often a neccessity in 3D printing. It is *most definitely* not a preferred choice, and it’s why 3D printing is roughly 25 years behind where it could have been. Because manufacturers keep filing and getting granted patents on incredibly basic mechanisms and mechanics, and they’re unwilling to license it out at costs that even top end enthusiast hardware could be able to bare. This hasn’t stopped, and as long as these practices continue and patent law remain as it is, we’re perpetually stuck 2 decades behind, expending most of our innovation and resources on reinventing wheels. Because we can’t legally make, buy or build upon the basic-principle wheels that already exist. For one maker, that might not be extremely consequential. But for anyone doing this professionally, or making commercial products – that’s their whole business on the line.
Here’s a DIY version made by Simon Vez and it works really well too. Latest tests claim in excess of 110mm^3/s !
https://youtu.be/GTeez9qmoKo
Impressive head, Vez3D is doing an amazing job at pushing his machine faster and faster!