What is plastic pellets mixing in extrusion?
As you might not know, a screw consists of three different zones:
- The feeding zone: Is responsible for solid conveying, moving the pellets down the extruder.
- The transition (compression) zone: Is responsible for removing the air from the mix while heating and melting the polymer.
- The metering zone: Is responsible for building pressure and stabilizing the flow output.
You can clearly see the three zones on the picture below, with a small addition on the “Maddock Mixing Screw.”

This mixing screw has a weird pattern added to the metering section. The goal is to mix the resin, homogenizing the melt. However, there is a downside to adding a mixing stage to the screw: the overall performance of the screw (torque requirements, heating due to shear, output) can be affected. There are many shapes and solutions that divide the melt and distribute the components, a few common solutions are presented below:
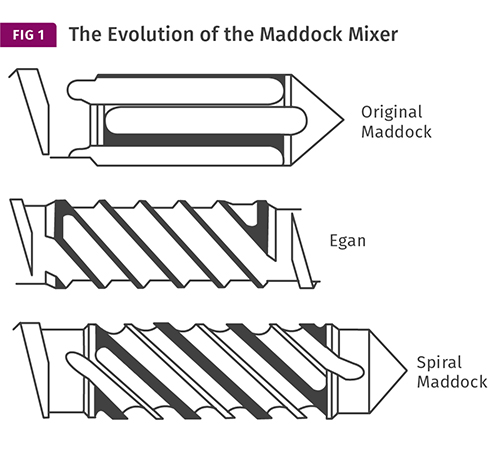
The preferred solution for plastic pellets mixing is definitely a twin screw. For instance, a pair of screws are co-rotating in order to greatly increase the mixing behaviour of the melt, leading to a very uniform output. This is the most common solution used by compounders, which is the specialization involving the mixing and preparation of special application resins (polymer with additives and filler for special application)

What are the advantages of pellets mixing?
By mixing polymers with different additives and fillers, you can get much more than with standard resins:
- Better printability
- Higher flow rate
- Higher stiffness
- Better look (colours)
- Physical properties such as: Food safe, flame retardation, UV tolerance, Antimicrobial
Compounding must be realized by a specialized company with their equipment. The end result is ready to use pellets with the Pulsar. Depending on the supplier, minimum order quantity can be as low as 25 kg.
Another solution is called the masterbatch. In short, this solution involves buying a concentrate of a mix and diluting it with a base resin. For example, one could buy a concentrate of pigments designed for PETG, and use a clear PETG resin as the base. In this case, the end user can get a colorized polymer and take the advantage of the low cost of clear resin. The ratio and the plastic pellets mixing uniformity must be clearly controlled.
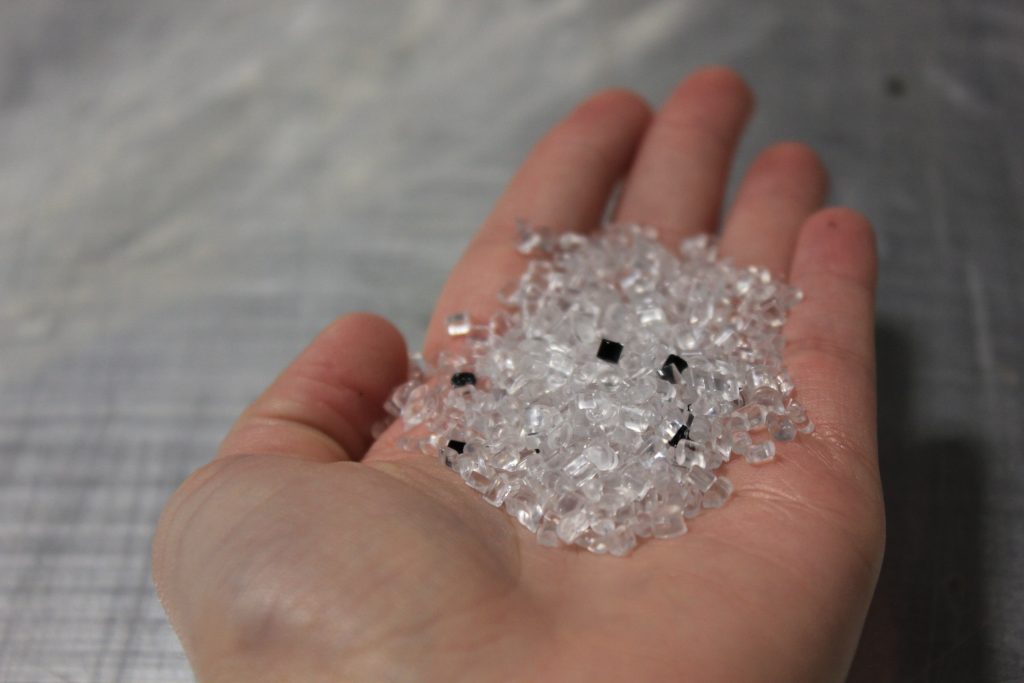
Pulsar screw design
To keep the Pulsar as light as possible, there are no mixing sections. Therefore, the screw length would also need to be increased with the addition of a mixing stage. So in theory, the Pulsar shouldn’t be able to provide proper mixing of the melt.
However, some experiments have shown that there is a good shear in the screw, and mostly in the later section of the Pulsar, thanks to the added anti-oozing mechanism. This section which is very close to the nozzle adds some mixing path and fixed separation of the melt before it exits, which greatly improves the mixing.

Result example using PETG
Thanks to our friend Guy from Cyrc Design who wanted to give it a try with PETG masterbatch. We weren’t sure at the beginning, as stated before, the Pulsar wasn’t designed for this application, but still, it could be worth a try.
We started with a simple line test to validate the colour uniformity. A few lines were stacked and we were amazed by the result; the colour was perfectly consistent, no change, no variations.
The single line test shows the brim which is a little thinner and the green/blue colour can be observed as it’s transparent. From this point of view, the stacked layers appear darker, but are similar to the brim when looked from the side.
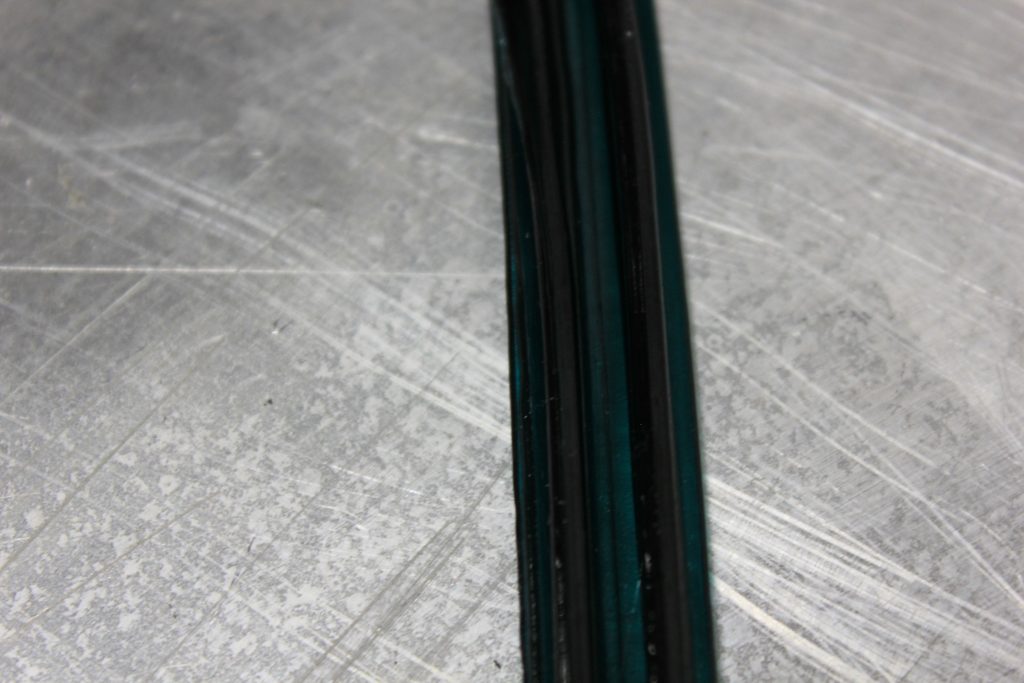
A thick walled part was printed with ribs in the center. Some light reflection can be seen where the transparency is shown at its best. Keep in mind that this current mix has only around 1.6% of colored pellets.
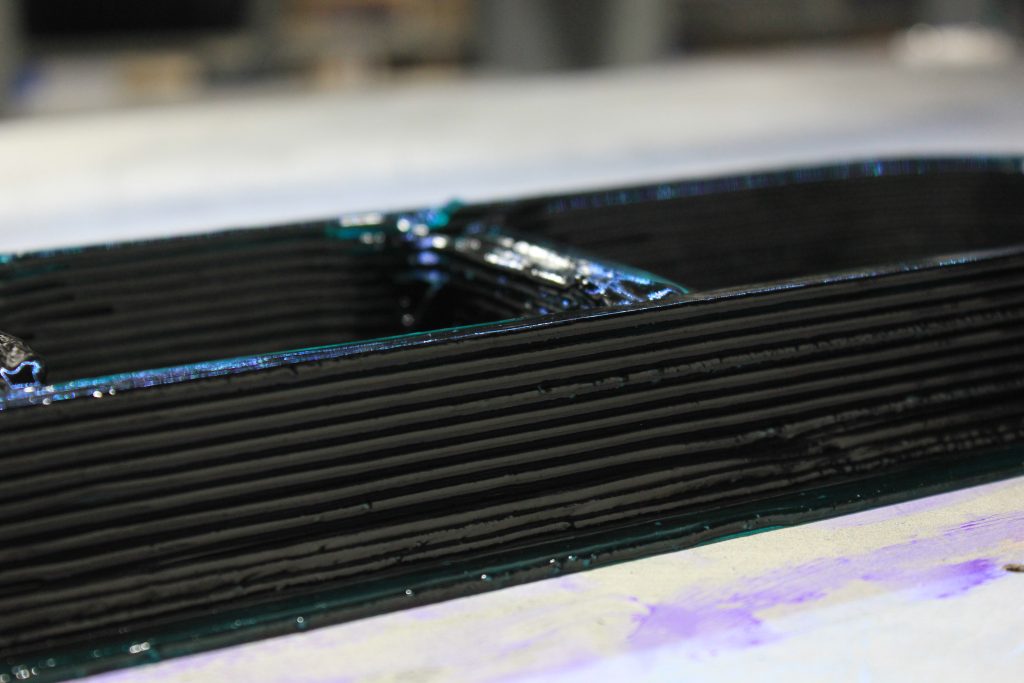
What’s the next step?
Well, now that we know we can mix colours, what about some fillers such as fibre or powders? Wood chips are very easy to get and can reduce the amount of polymer required for a print, it could be worth a try mixing them with reprocessed pellets.
Source:
http://extrusionist.com/extrusion-processes/single-screw-extrusion.html
https://www.thermopedia.com/content/753/
https://www.ptonline.com/articles/extrusion-barrier-screws-and-mixers
https://en.wikipedia.org/wiki/Plastic_compounding
https://phoenixplastics.com/plastic-compounding-the-purpose-and-benefits/