Choosing a filament size can seem like a tough decision when designing a 3D printer. It is not only a question of personal taste, there are advantages to both standards. Keep reading if you wish to know more.
A bit of history
The first extrusion printer was released in 1991 by Stratasys as the « 3D-modeler ». They released the FDM series printers soon after: 1650, 2000 and 3000. Based on their manual, these printers were based on 70mil (1.78 mm) filament. Despite many sources claim that 3.00mm existed before 1.75mm from plastic welding suppliers, Stratasys used a standard much closer to the 1.75mm filament before the RepRap era. It is true however that the open-source community adopted the 3.00mm in its early days.
Released in 2009, the MakerBot Cupcake CNC was using 3.00mm filament. Ultimaker released their Ultimaker Original in 2011, also based on 3.00mm filament.
Many sources claim that 1.75mm filament was getting more and more popular since 2011. As the popularity increased in 3D printers, it is possible that more and more third party started making filament for Stratasys printers, which could also be adopted by the open source community.
Why are both standards still used? What are the differences, advantages, and disadvantages between the two sizes?
A matter of habits
People who already have a 3D printer are used to a specific size and there is a high chance they might want to stick with it. Any justification can be valid for choosing a certain size:
Why would I change something that is working?
I already have a bunch of 3.00mm spools, I don’t want to throw them away!
1.75mm is too small and easy to break!
3.00mm is too stiff and hard to manipulate!
It is hard to convince anyone against their will. If you’ve never experienced any of these sizes or you are still hesitating, below are much more interesting comparison facts!
Performance
Pressure
While printing, your extruder is fighting against pressure to generate an output flow of molten plastic. If the pressure is too high, either your extruder motor will skip steps or it will grind your filament. Plastics behave very differently than most liquids such as water and alcohols when it is in a molten state. It is called a non-Newtonian fluid. Its viscosity decrease with the increase of shear strain, meaning that flowing at higher rates can be easier than at slower rates.
However, in 3D printing applications, we don’t see this behavior. Viscosity also depends on temperature and extruding faster also mean that we give less time for the filament to melt. The higher flow means lower extrusion temperature (even if your sensor tells you that your heat block is reading the same temperature) thus higher viscosity and pressure.
Water analogy
Pressure increase due to a change in the section is well known is water and air duct systems. This pressure can give us a very rough idea of the effect of a viscous flow. However, please note that this is not the optimal method to calculate the pressure loss for a plastic as many simplifications have to be considered.
At the bottom of the nozzle, the diameter will change from a large section to a very small orifice, which is your nozzle diameter. The most common nozzle size is 0.40mm. Let’s consider this size for our calculations with an angle of 90° at the bottom of the tip.
The following formula is used for finding a K-value, an empirical factor that will allow us to compare the effect of filament size on pressure.
Based on this simplified formula, we can see that the pressure factor will be higher when going from 3.10mm down to 0.40mm compared to getting from 2.00mm to 0.40mm.
Piston analogy
Pressure is the result of a force applied to a surface:
If we compare both filament size and consider they require the same pressure to output the same flow, we can consider:
Thus,
Simplified,
If we wouldn’t consider the Reynold number and the pressure drop caused by the change in diameter, a 3.10mm piston requires 2.4 times more force to generate the same pressure as a 2mm would do. The piston reference is actually what is happening inside a hotend. The filament will soften and form a plug, matching its diameter to the interior diameter and pushing the molten plastic below.
Numerical analysis
After configuring the correct PLA material from data, a simplified nozzle and heat-break were used for a flow simulation. This shows a closer representation of what is happening in term of heat and pressure.
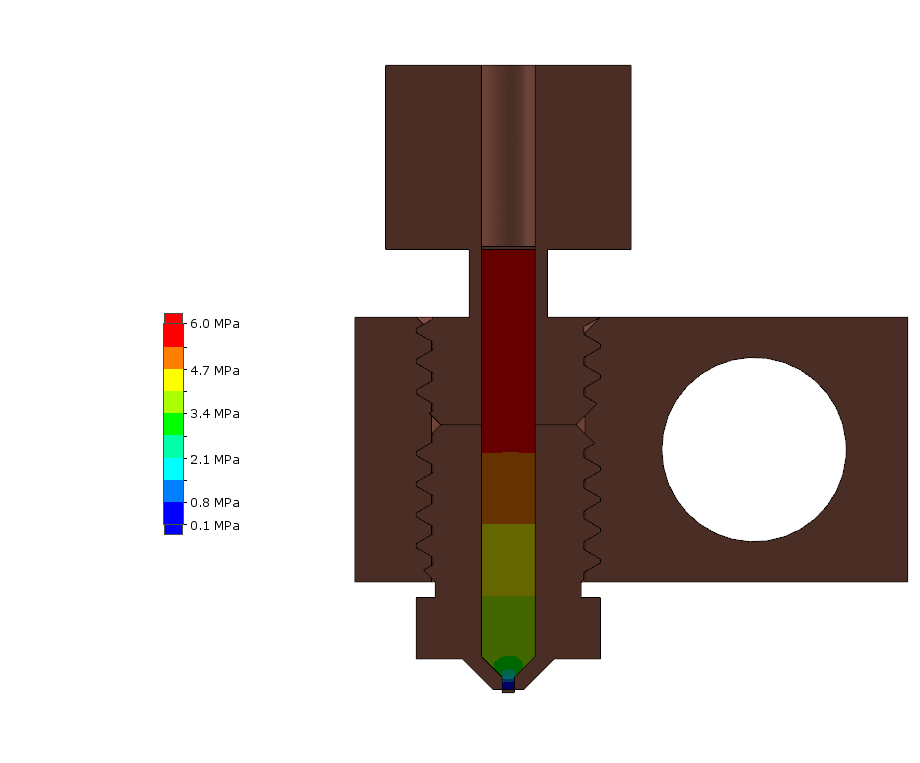
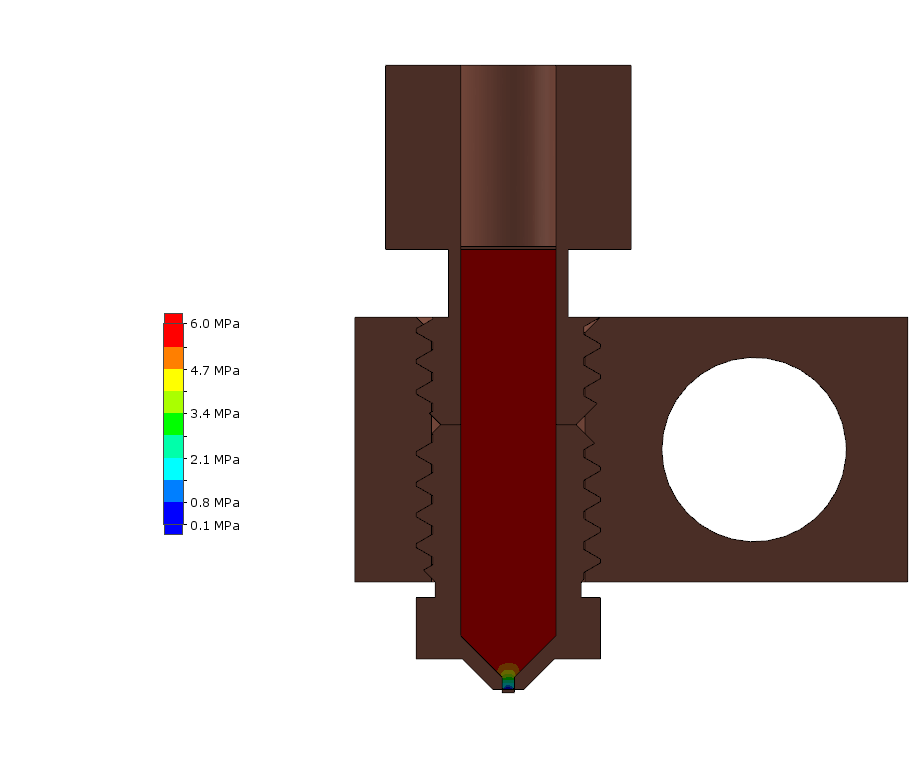
The analysis shows that the pressure is about 1.63 times higher with the 3.00mm, so the force required is 3.92 times higher.
Polymers are bad heat conductors. For example, PLA has a thermal conductivity of 0.11 W/mK at room temperature and 0.19 W/mK from 150°C up to 230°C. This is quite low compared to copper ( 385 W/mK ) !
Once the filament reaches the melting zone, the outer shell will start absorbing heat from the nozzle. The good insulation properties of plastics will prevent heat from getting to the core of the filament. The thicker the filament is (larger diameter), the harder it is for heat to reach the center.
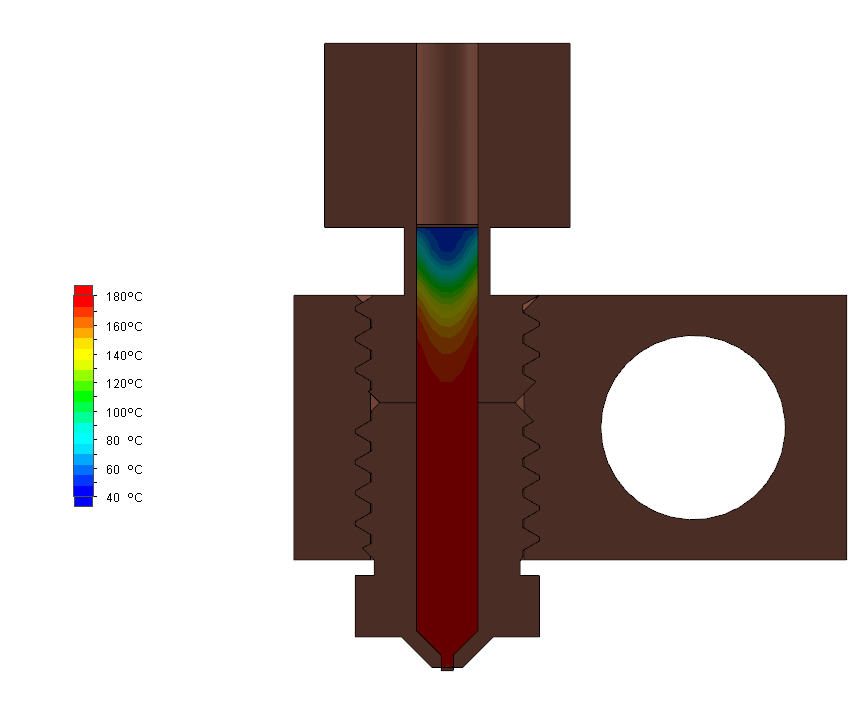
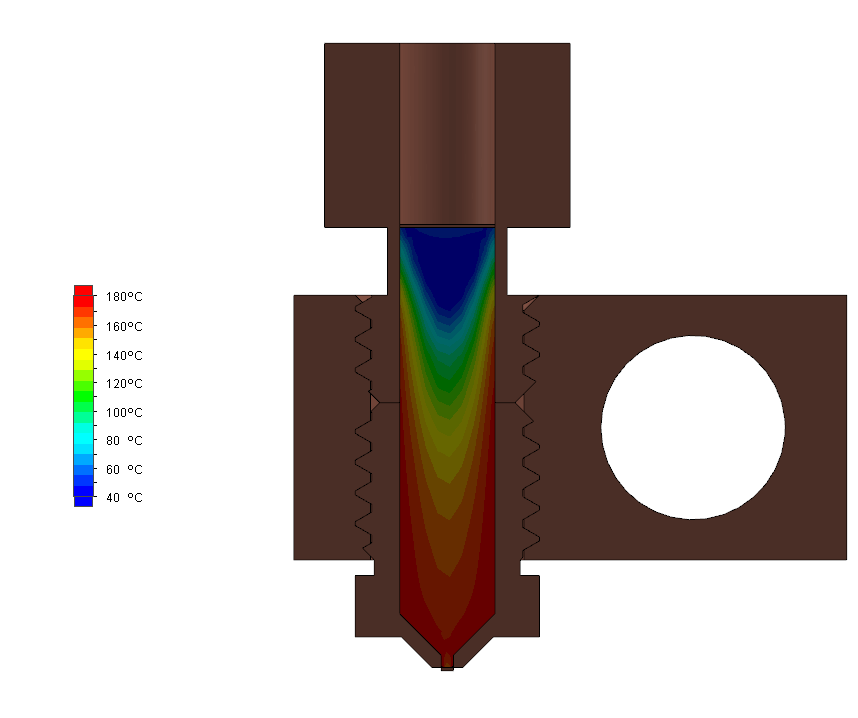
1.75mm
- Requires less force
- Heat more efficiently
Printing
Print size and precision
Precision is required when you want to print a very fine detail, i.e. when using a 0.20mm nozzle. With the very high force and pressure requirement of 3.00mm filament, is it not practical to have such a small nozzle with this set-up. The print speed must be reduced and the extruder needs to be very powerful. 1.75mm filament is better for finer details when reliability and extruder efficiency is important.
If you wish to print using a 2.00mm diameter nozzle, your only choice is obviously 3.00mm filaments. A 1.75mm would require a more complex nozzle design to accomplish the task of being able to output larger than its diameter.
When it comes to printing fast, it does not always depend on the nozzle size, the layer height, or the printing speed. It is a mix of all these settings that will determine a volumetric flow. Due to the better heat transfer efficiency from 1.75mm, this filament size is able to output a higher flow when compared to a 3.00mm hotend with the same form factor. Both filament sizes would benefit from a longer melting zone, so it is hard to judge without further testing.
The graph below shows a comparison flow test made on both 1.75mm and 3.00mm filament. The nozzle size is 0.80mm. The same filament manufacturer, type, and color were used for both tests, such as the same extruder. The pressure increased very quickly after only 6mm^3/s and the extruder wasn’t able to push the filament faster.
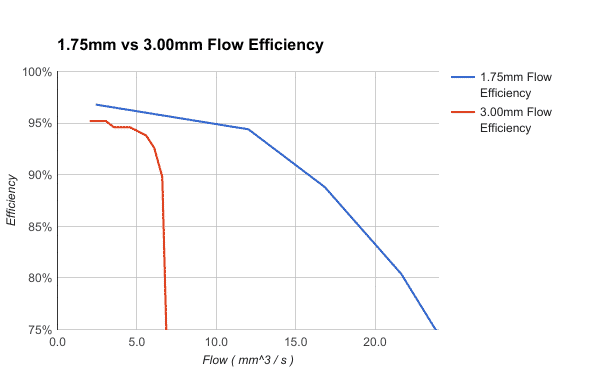
Experimental tests comparing 1.75mm and 3.00mm filament
Enclosed environment
As previously mentioned, the 3.00mm filament is harder to heat up to its core. It might reduce the maximum possible flow rate, but it has some advantages too. When printing in an enclosed environment, the filament will be subjected to a bit of heating through convection with the ambient air. When printing at a temperature close to the glass transition temperature, one filament might become a bit soft.
Ther higher mass and volume ( thermal inertia ) allow the 3.00mm to stay for a prolonged period of time before getting softer.
For the same extrusion speed, the 1.75mm filament will move 60% faster, so inherently stay for less time inside the heater chamber.
The filament softening is a very complicated variable to measure and validate because it depends on many factors:
- Printer size
- Filament length inside the heated chamber
- Heating time
Flexible
Flexible filaments are quite tricky and most problems are related to the extruder. It must be carefully guided through the extruder driving mechanism. The compression force will quickly buckle due to the material high flexibility. It is also harder to grip and tend to slip more than other types of filament.
The 3.00mm will definitely be easier to work with and will be more tolerant to a poorly designed extruder.
1.75mm filament will require a better-designed extruder but will allow faster extrusion speed and details.
1.75mm
- Can print faster
- Can print small details
3.00mm
- Can print larger line width
- Stay strong longer under heat
- Flexibles are more permissive
Acquiring filaments
Filament manufacturer
From a filament manufacturer point of view, the filament requires roundness and proper diametral dimension. These results will have different behavior based on the filament standard extruded.
The whole process starts from pellets inside an extrusion machine. The plastic beads go through a progressive heating and compression before exiting a final die where it gets its round shape. The process is quite the same for both 1.75mm and 3.00mm.
From the feedback and experience of filament manufacturer, it is much easier to get good roundness and tolerance with 3.00mm filament. As this size is bulkier, the small variation in the extrusion system will be less noticeable compared to a 1.75mm filament. While being bigger, this filament has a little bit more of margin too in term of diameter; a difference of 0.03mm is less critical than the same difference for a 1.75mm filament.
Sadly, despite being easier to control, the price is the same for both filament, so this isn’t a direct advantage for end-users.
Specialized filaments such as engineering plastics and filled (carbon fiber, glass fiber, etc) are easier to manufacture in 1.75mm, thus explaining why they are hard to find in 3.00mm diameter filament.
2.85mm or 3.00mm?
It might be a bit confusing to order 3.00mm filament for your printer since there are two standards for this filament:
- 3.00mm filament that is actually 2.85mm
- 3.00mm filament that is actually 3.00mm
The most common size is 2.85mm, but it will be very often called 3.00mm.
Specialized filament suppliers will always clarify this diameter. However, some general filament store might not have the exact detail, so be aware when you are ordering this filament size.
Conclusion
In conclusion, if you are looking for speed, performance or details, 1.75mm is the way to go. It’s an all-around filament, simply.
If you are looking for massive line width, 3.00mm should be your preferred choice.